An insidious threat: corrosion risks in data center air conditioning
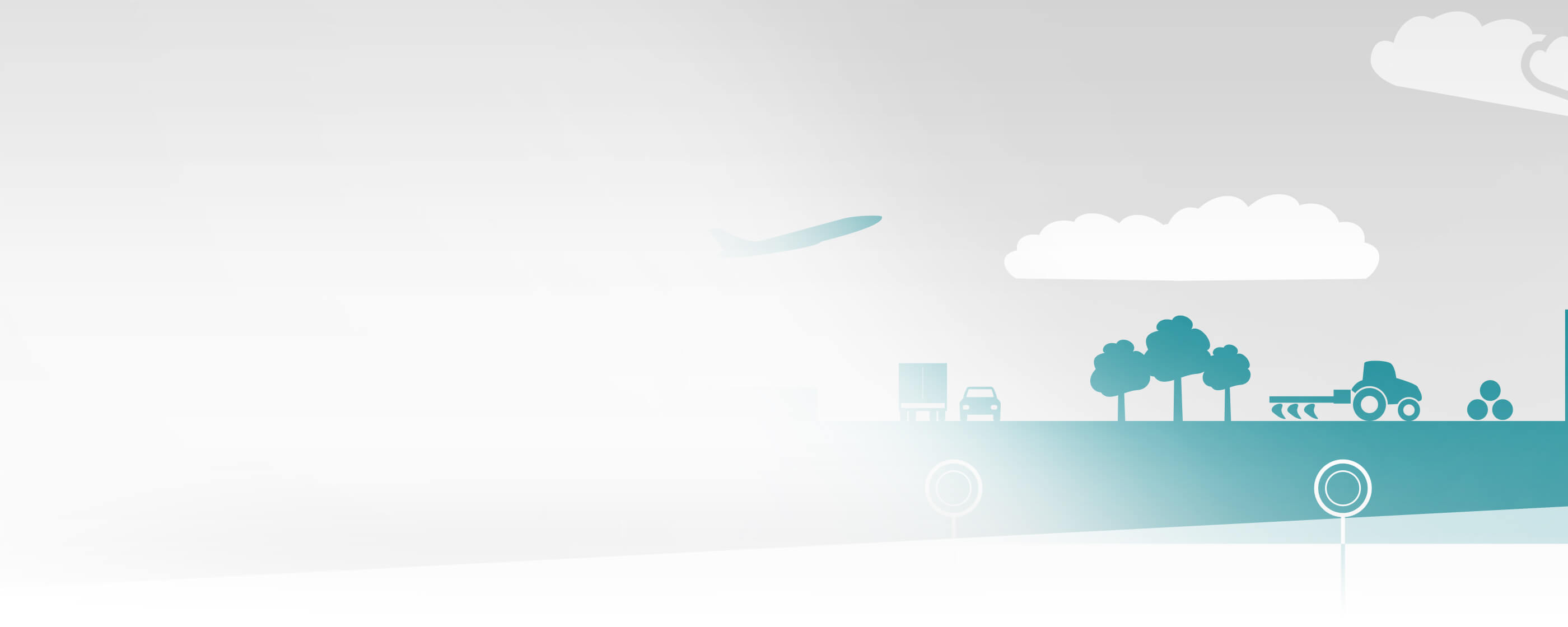
Corrosion risks data center
Heat exchangers in Free Cooling systems are among the most mission-critical components in a data center. As air/water heat exchangers are directly exposed to emissions from the outside air, they are often at risk of corrosion and soiling. A basic understanding of the various measures available to protect air/water heat exchangers from corrosion and of the corrosive processes taking place in the chilled water circuit can really help data center businesses to protect their investment.
In data center air conditioning, even minor problems can have huge consequences. Therefore, the IT sector has established availability classes whereby redundancy is achieved with double or multiple duplication in the system, to reduce the risk of failure to a minimum. Both design and maintenance/service measures are necessary to achieve an effective availability strategy. Leakage monitoring, regular filter replacement and the cleaning of heat exchanger surfaces should all take place as a matter of course. In addition, data center operators must also get to grips with corrosion protection if they are to ensure operation that is both energy efficient and reliable. Corrosive processes in the cooling and air conditioning system are often neglected, but a basic understanding of them can provide lasting protection against nasty – and costly – surprises. Since all air conditioning components are exposed to corrosive processes to a greater or lesser extent depending on the environmental conditions, it is often only a matter of time until measurable changes occur in important components. However, choosing the right type of corrosion protection can help data center operators to extend the service life of precision air conditioning units and reduce unscheduled downtimes.
Basic principles behind corrosion formation
In physical terms, corrosion describes the measurable reaction of a metal with its environment. In most cases, the result of this reaction is a gradual, insidious process, which over time can lead to impaired function of a component or even an entire system. Corrosive processes are triggered by chemical or electrochemical substances in the ambient air, or by contact between two different metals. Although corrosion essentially occurs everywhere, unfavorable environmental conditions can of course drastically speed up the slow, natural degradation process. In chilling systems, for example, pipes and fins in heat exchangers are continuously exposed to the outside air, which makes them fundamentally more susceptible to corrosion. In this respect, corrosion can have a severe impact on the performance of refrigeration systems. If environmental conditions are particularly unfavorable, heat exchangers may suffer such severe damage that they become deformed, or individual fins break. If this happens, blockages in the air flow or a reduction in the effective heat exchanger surface diminishes the efficiency of the refrigeration system. Moreover, once damage to the material structure has occurred, it is often irreversible and necessitates major repairs or even a replacement.
The most common forms of corrosion encountered in the field of cooling and air conditioning is oxygen and acid corrosion. Oxygen corrosion is caused by metal reacting with oxygen and forming oxides. If copper or aluminum is used, the resulting natural oxide layer protects the interior of the metal, so that in this case, oxidation can actually be regarded as beneficial. However, forms of acid corrosion are considerably more aggressive than oxygen corrosion processes. Where major industrial processes are taking place, emissions can significantly speed up the rate of corrosion. Compounds such as nitrogen oxides and sulfur oxides, as well as ammonia, chlorides, and carbon monoxide, react with copper and aluminum and form acids that can lead to microscopic cavities in the material. This process is also known as “pitting” and can cause severe corrosion damage in just a few months. The greatest risk factors that may speed up the corrosive degradation process can be found in areas with heavy industry, a high traffic density, or in the immediate vicinity of agricultural land.
As soon as more than one type of metal is used in a refrigeration component, a system can be subject to what is known as galvanic corrosion. In conjunction with an electrolyte such as salt water, ions from a “less noble” metal start to flow in the direction of a “more noble” metal. At some point, this process degrades the metal that is releasing ions. This phenomenon particularly affects copper-aluminum components and combinations of metals in environments with a high salt water load. Galvanic corrosion can cause considerable damage to aluminum microchannel coils with copper pipes, in particular. Then, fractures or blockages in the fine microchannels cause partial pressure drops or even result in refrigerant leakage. The risk of corrosion is additionally augmented by other factors such as the use of sub-standard metals. Moreover, fractures and cavities in the surface can catch more water and accelerate the degradation process. The general corrosion risk also rises in hot and humid climates and in fluctuating temperatures.
Methods of corrosion protection and their benefits
Thanks to state-of-the-art process engineering, today there is a wide range of possibilities for effectively protecting heat exchangers against corrosion. Each method has its own advantages and disadvantages. For example, the use of thicker aluminum fins will provide protection against premature fin fractures and is even relatively inexpensive to implement. The additional material slows down the impact of corrosive processes on the material structure, thereby prolonging the time until a fracture occurs. However, when the system is in operation, the increased fin width reduces the airflow and therefore the efficiency of the heat exchanger. The use of Cu/Cu coil fins is a better option. These enable the impact of galvanic corrosion to be completely eliminated, as the pipes and fins in the heat exchanger are made entirely of copper. What’s more, the heat exchanger also retains its heat conductivity properties. The main disadvantages of this method are the higher material costs involved, and insufficient protection against oxygen corrosion.
In addition to structural measures, coating techniques can also help to protect against corrosion. Here, state-of-the-art top coats are applied directly to the surface of heat exchanger components using pressurized spraying systems. A non-reactive resin such as epoxy is often used here to protect the metal components against acidic solutions in the atmosphere. The spray-on coating provides protection against all types of corrosion and is relatively inexpensive compared with other types of coating. However, the relatively thick coat produced as a result is less energy efficient and negatively impacts on the system’s heat conductivity, reducing the efficiency of the chilling system. Additional pressure drops also increase the fans’ power consumption. Therefore, special epoxy resins make use of aluminum-pigmented polyurethane. Used appropriately, the material itself offers outstanding protection. It can also be applied very evenly, with extremely uniform individual layers. However, all spray-on coatings run the risk of gaps in the top coat. With the spraying method, these gaps can never be ruled out entirely and will make it easier for pitting corrosion to occur. Spray-on coatings are therefore recommended for conventional installation conditions, and are less suited to locations with very high environmental loads, due to the weaknesses described above.
Unlike spray-on coatings, cathodic dip coating ensures very uniform layers. With this method, the heat exchanger is electrically charged and then fully immersed in a chemical bath. As a result, the coating adheres evenly to all surfaces. If the components are then mounted with due care and attention, no gaps in the protective coating should be expected. As well as ensuring a very uniform result, i.e. layers of very even thickness, cataphoresis also produces the thinnest protective layer of all coating methods and has only a minor impact on heat conductivity. The special ElectroFin method additionally uses cationic epoxy polymer, which is applied using the cathodic dip coating process and provides outstanding protection against all types of corrosion. However, the drawback of this technically complex coating process is its greater expense.
Overview of different corrosion protection methods for microchannel coils
MethodUniformityLayer thicknessSalt spray testLoss of heat conductivityAdditional costs
Thicker fins | - | - | - | ~5% | Low |
Cu/cu coil fins | - | - | - | ~0% | Medium |
Spray-on coating (epoxy) | OK | 50-70 μm | 1,500+ hours | ~3-5% | Medium |
Spray-on coating (pigmented epoxy) | Good | 25-30 μm | 11,000+ hours | 0-3% | Very high |
Cathodic dip coating (ElectroFin) | Very Good | 15-25 μm | 6,000+ hours | 0-1% | High |
The above comparison of the various corrosion protection methods enables a number of key conclusions to be drawn regarding use in practice. A spray-on coating with aluminum-pigmented polyurethane offers the most effective protection on account of the very good results obtained in the salt spray test. However, it still entails the risk of localized gaps. Therefore, despite obtaining a worse result in the salt spray test, cathodic dip coating (e-coating) is the most impressive method – due above all to more reliable coating technique used. Although an epoxy resin coating performs worse than other methods in terms of reduced performance and effectiveness against corrosion, it is far less expensive.
Structural measures such as Cu fins/pipes and wider aluminum fins are relatively simple to implement in manufacturing terms. But although wider aluminum fins are the most affordable solution, they are also the least reliable. For this reason, thicker aluminum fins should preferably be used in combination with other types of protection. Cu/Cu coil fins are relatively expensive and offer only a limited benefit compared with aluminum fins. As they primarily protect against galvanic corrosion, they are especially suitable for systems located in close proximity to the sea.
Location conditions and protective methods
Location conditions | Corrosion factors | Suitable protection method | |
Airport/Heavy Traffic | General corrosion from NOx, SOx und CO | Spray-on coating or e-coating | |
Industry | General corrosion from NOx, SOx, CO, ammonia, chlorine, etc. | Spray-on coating or e-coating | |
Close proximity to the sea | Galvanic corrosion caused by a high concentration of salt water | Cu/Cu coil fins | |
Coastal area | Galvanic corrosion caused by a low concentration of salt water | Cu/Cu coil fins, spray-on coating or e-coating | |
Agriculture | General corrosion from NOx, SOx and ammonia | Spray-on coating or e-coating | |
Combination of location conditions | Galvanic and general corrosion | High-quality spray-on coating or e-coating |
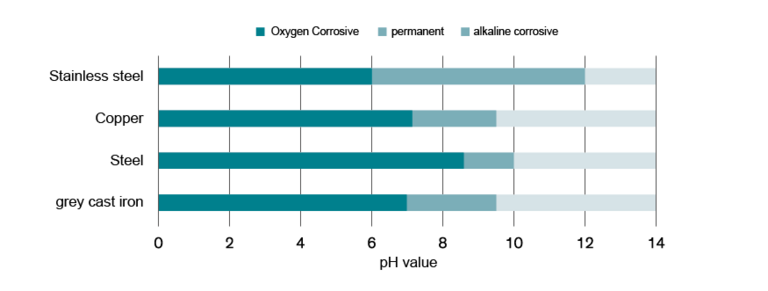
The importance of water quality
As well as assessing the on-site corrosion risks for the air/water heat exchangers used, continuous monitoring of the prevailing water parameters in the chilled water circuit is also vital for preventive corrosion protection. The fact is that plant operators who continually keep an eye on water quality – right from the time the system is first filled – not only improve their system’s general service life, they also reap the long-term benefits of higher efficiency. The type of refrigeration system is also an important factor here. In data center air conditioning, two different water-cooled system designs generally predominate: precision air conditioning units with integrated DX refrigerant circuit and water-cooled condenser, or chilled water indoor units that are connected via heat exchangers to a central chiller. In both models, the water circuit must be rich in oxygen and kept free from foreign matter and sediment to ensure a long service life and unrestricted function. Current research projects show that closed circuits in chilled water and liquid cooling systems can suffer their first corrosion damage within just one or two years. This is a problem not just due to damaged pipes and eventual leakage, but also because flaked off particles of corrosion can easily clog pumps, filters, and the capillary tubes of heat exchangers. A practical guide to producing and maintaining optimum water quality is available from the Bundesindustrieverband technische Gebäudeausrüstung (German Federal Industrial Association for Building Services, BTGA). BTGA Rule 3.003 describes the general procedure in this field, and covers important aspects such as water composition, maintenance, and quality control.
The quality of the water in the circuit is fundamental to comprehensive corrosion protection, as this directly influences the risk of corrosion damage. However, water quality cannot be assessed merely on the basis of a single parameter; rather, water composition can be interpreted entirely differently depending on the intended purpose and the conditions. The corrosivity of a particular water mixture is not classed identically for every material and cooling circuit. Most water circuits make use of a mix of materials with very different chemical properties. The most common constituents are black steel, copper, stainless steel, gray cast iron, aluminum, silver solder, and rubber seals. In most cases, advance corrosion prevention through design – by using harmonized materials, for instance – is extremely expensive and unfeasible. Therefore, the question is how to best protect the system against corrosion. Often, the only sensible and also easiest method of corrosion protection in chilled water systems is simply to continually check and adjust the water conditions.
Common types of corrosion in the chilled water circuit
-
Oxygen corrosion is caused by dissolved oxygen in the water. It disappears over time in closed systems, but a residual content of oxygen must be reckoned with. If oxygen, water and metal (mostly iron) react with one another, the metal will suffer oxidation or corrosion.
-
With acid corrosion, an excessively low pH value (<5 pH) causes acid to attack the metal, corroding it or splitting it into ions, ultimately forming elementary hydrogen. This reaction can take place without oxygen, and the more acidic the environment, the faster and more aggressive the process.
-
Electrochemical corrosion is also referred to as galvanic corrosion. For this to happen, two dissimilar materials with different positions in the electrochemical series must be in contact with one another. The less noble metal releases electrons and oxidizes. The result is the constant degradation of the material. The further apart the metals in the electrochemical series, the faster and more aggressive the corrosion process. Water and the minerals it contains act as a conductive medium.
-
Bacterial corrosion can also occur without oxygen. Bacteria draw electrons out of the metal, causing it to oxidize. Sulfur oxide is produced as a waste product of the bacteria, which provokes a strong odor in the surrounding fluid and can be an indicator of a bacteriological load.
Oxygen content is a factor with huge consequences for potential corrosion processes in the chilled water circuit. If the water has a high percentage of oxygen, we can also expect a higher corrosion risk. In closed systems, the oxygen dissipates rapidly, however. Oxygen can also be chemically bound in order to prevent oxygen corrosion. But there are other factors that also determine the corrosivity of the water in a circuit. These include the water’s pH value, hardness and conductivity.
Assessment criteria and quality considerations
The pH value is the measure of an acidic or base aqueous solution. Tap water has an average pH value of 7.5. Both an overly high and an overly low pH value should be avoided. Different materials have different pH value ranges, within which they are able to form a protective oxide layer. If an installed material is above or below this range, the risk of corrosion increases dramatically, leading to acid corrosion as mentioned above. The difficulty with pH values is that after a system has been filled, the water in the circuit still contains a high proportion of dissolved carbonic acid. This gradually escapes as carbon dioxide – but then the lack of carbonic acid causes the pH value to rise. It is therefore almost impossible to adjust the pH value precisely. If the pipe network contains a mix of materials, this considerably narrows the range within which the pH value will not provoke corrosion in the components. This is clearly illustrated in the diagram below.
The hardness of the water is determined by its content of alkaline earth metal ions. There is carbonate hardness – also referred to as temporary hardness – on the one hand. This is chiefly caused by cations of magnesium and calcium. On the other hand, there is also a element of permanent hardness, which cannot precipitate as an insoluble solid. In warm parts of the circuit, the non-permanent hydrogen carbonates, which are dissolved in the water when a circuit is filled, precipitate as carbon dioxide and carbonates. The result of this combination is commonly also referred to as “limescale”. This substance adheres to the inside of heat exchangers and pipes, leading to huge losses of efficiency in the entire system.
The conductivity of the water is determined by the quantity of dissolved anions and cations it contains. These include hardness builders such as magnesium, calcium and hydrogen carbonate, but also minerals and dissolved metal ions. The more particles the water contains, the higher its conductivity and therefore its susceptibility to electrolytic corrosion. Moreover, this increases the likelihood of sediments in the water. The best known exponent of this is limescale, which always forms at the warmest point with the slowest flow in a chilled water system, which in most cases is the heat exchanger. There is now an acute risk of the heat exchanger clogging, which has a hugely negative impact on efficiency. This is because of the smaller contact surface and the fact that limescale has a far lower thermal conductivity coefficient than copper. Partial limescale deposits can also cause stress cracks in the heat exchanger due to the varying heat expansion. High conductivity does not necessarily constitute a higher risk, however. Corrosion inhibitors increase conductivity, for example, but in this case it is not problematic.
When checking the water conditions, particular attention should also be paid to minerals. Dissolved minerals are especially critical for the chilled water circuit, because they are highly reactive and provoke both precipitation and corrosion. Chloride is the salt produced by hydrochloric acid and is the most stable parameter in the circulatory system. It is primarily used as a chemical catalyst, but it also intensifies corrosive processes. During this acceleration, chloride is not used up, however, but retained. In addition, chloride attacks the passive layers on metals, exposing more of the surface to attack from normal oxygen corrosion. In certain conditions, chloride can also cause local damage that results in pitting corrosion.
Sulfate is the salt produced by sulfuric acid and acts as a nutritional base for any bacteria in the circulatory system. These are then sulfate-reducing bacteria. The combination of calcium and sulfate to form calcium sulfate can also be an indicator of sulfate reduction. Generally, these very hard deposits are responsible for poor temperature transitions and inefficient operation.
Bacterial processes cause nitrate to transform into ammonia and to react with copper pipes to form a copper ammonia complex, which is capable of oxidizing iron without a supply of oxygen while disintegrating back into ammonia and copper. Through the process of complexing, ammonia therefore continually oxidizes the iron constituents of a circuit. Tap water mostly has a low nitrate value, and in technical use can be regarded as critical from approx. 5 mg/l. However, the nitrate level is becoming increasingly relevant in the evaluation of corrosion risks, due to the rising concentration of nitrate in the groundwater, particularly in agricultural areas.
Acid corrosion in water-glycol mixtures
To prevent the pipework from freezing, outdoor water circuits – connecting an outdoor chiller to a CRAH, for example – are filled with a water-glycol mixture. However, in certain circumstances glycol can intensify the corrosive properties of the circuit water. If there is dissolved oxygen in the water, the glycol can decompose, producing acids that acidify the water-glycol mixture, i.e. lowering the pH value. Acidification of the mixture can lead to pH values of less than 4. Consequently, as well as the usual corrosion inhibitors, antifreeze concentrates also contain acid neutralizers, which can mitigate the acidification to a certain extent. There is only a limited amount of these acidic buffers in the mixture, however, which is why the pH value and glycol content need to be checked regularly. Furthermore, if the glycol concentration falls below the minimum value specified by the manufacturer, increased bacterial growth can be expected. This results in organic deposits that can form the basis for bacterial corrosion. Common minimum levels are 20 percent by volume for ethylene glycol and 25 percent by volume for propylene glycol. Here, it may be a good idea to contact the glycol manufacturer and read the manufacturer’s technical data sheets.
Conclusion
Today, precision air conditioning systems carry out key mission-critical tasks over long periods of 10 to 15 years. Therefore, an appropriate service strategy plays a crucial role in maintaining the system’s performance over the long term. For this reason, a comprehensive maintenance strategy should include corrosion protection, in addition to the mandatory leak tests. Inspecting the system regularly will not only maintain the efficiency of the air/water heat exchangers, it will also significantly prolong the service life of the entire system. To improve corrosion protection for the long term, we recommend removing coarse dirt such as leaves, pollen, and dust from the heat exchanger surfaces at regular intervals using an industrial vacuum cleaner. The coating must then be thoroughly inspected for soiling and damage. Fine dirt and matter adhering to surfaces are best removed using a jet wash or water from a hose. If you use additional detergents, also ensure that the detergent and coating are compatible with one another.
In addition, plant operators should also get to grips with water quality and the recommendations from BTGA Rule 3.003, which are extremely pertinent to data center cooling systems. Although specific recommendations will vary depending on the situation, it is universally the case that the oxygen content of the circuit water should be monitored regularly. Furthermore, chlorides and sulfates must be reduced in line with BTGA Rule 3.003, and the use of water with a low mineral content is also generally recommended. Moreover, the pH value should be kept at a medium level, in line with specific material resistance. Further recommended measures include softening and residual hardness stabilization. However, the use of demineralized water tends to be viewed as disadvantageous, because it is acidifying and highly reactive.